Further Information
Operations Optimisation
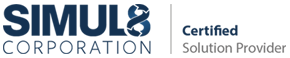
Quality, cost and delivery (QCD) are key standard metrics used by manufacturing organisations all over the world. Prime Design work in partnership with our customers to help ensure a positive performance against these metrics and support their continued success. We have over 150 years of combined experience in FMCG operations so have a wealth of expertise to support these optimisation activities. Services that we offer are as follows:
Simulation Modelling – Prime Design can run a range of scenarios to establish the optimum arrangement for a manufacturing process. Altering all the relevant parameters in the process, such as activity and equipment speeds, conveyor lengths, accumulation capacity and staffing levels we can run operational simulations to assess relative impacts. These simulations provide realistic outputs, and efficiencies are also determined by taking into account % rejects, mean time between failures (MTBF) and Mean Time To repair (MTTR).
Having the opportunity to optimise a process (virtually) before implementation helps our customers establish the right solution (layouts, speeds staffing…) in a safe environment. This avoids unnecessary rework, additional cost, lost time and reduces risk.
Manufacturing Operations Survey – This popular service includes a brief site survey to review manufacturing systems and the preparation of a summary recommendation report. This service will critically review your manufacturing operation and highlight observed positives and suggestions for improvement. We often find that organisations value having an external (non-biased) perspective on their operation as this minimises internal conflicts created by the findings!
Continuous Improvement – Prime Design is also able to support its customers with implementing Continuous Improvement (CI) frameworks. We have many experiences of successful implementation of these processes and the benefits and infectious enthusiasm they create when implemented well.
Prime Design advocate using a structured basic framework that is easy to understand, universal and effective. We believe that the value is not in the process itself but in the reaction created within an organisation and the possibilities this presents. For the CI framework to generate the expected reaction, our customers will commit ongoing genuine management support and time but the impact of these small investments can be truly transformational.